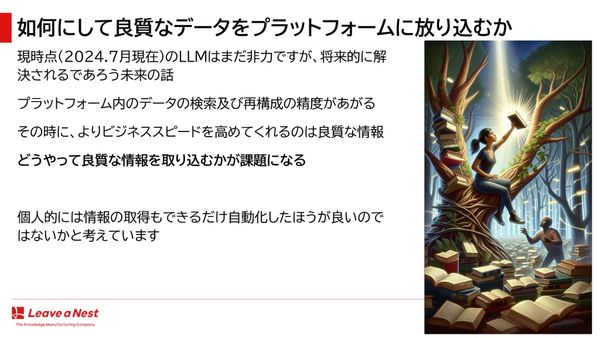
2024.10.01
自社の社内情報を未来の“ゴミ”にしないための備え 「情報量が多すぎる」時代がもたらす課題とは?
提供:株式会社ABEJA
リンクをコピー
記事をブックマーク
村田宗太氏:使用したモデルですが、Auto Encoderになります。実際にはAuto Encoder以外の手法も試してきていますが、冒頭で説明した通り弊社の不良は最終工程の段階では非常に少ない頻度でしか発生しません。
裏を返せば良品データを大量に入手することは可能です。このことを踏まえ、正常画像のみでモデル構築ができることがメリットとされるAuto Encoderを使用することとしました。
一方で良品といっても鍛造工程で完成されるギヤのため、歯底部分の表面や歯先の形状にわずかなばらつきがあります。そのため大量のデータが必要になります。
Auto Encoderについて簡単に説明したいと思います。Auto Encoderは正常画像のみで学習していますが、学習データをもとにその特徴を捉えて学習データセットに似たデータを復元するアルゴリズムになります。
正常画像を入力した場合、モデルは入力した特徴から正常画像に似た画像を生成します。逆に不良画像が入力された場合にも、モデルは入力した特徴から正常画像に似た画像を生成します。
不良画像のみの場合は入力画像と復元画像に差分が発生するため復元できない特徴を認識し、欠陥を検出することができます。
「学習したAuto Encoderモデルは本当に正しく判定できるのか」という疑問が残ると思います。そこで先ほどアノテーションを行なった不良データにて確認をいたしました。
こちらAuto Encoderの性能検証結果です。
今回の検証はたくさんある不良の種類の中から最も発生頻度の高い打痕を対象に検証を進めています。
コンフュージョンマトリックスで表現させていただいていますが、入力がNG品の場合、きちんとNG判定した割合が98パーセント。逆に入力がOK品の場合、きちんとOK判定した割合が61パーセントになりました。
現場の話で言うと、NG品を確実に検出することがなによりも大切なため、ここが高い精度で判定できていることが確認できたのは現場実装の可能性を感じる大きな成果でした。
一方で、OK品の判定率は現段階ではやや低く感じます。この判定率はAuto Encoderにかける学習画像のデータ数を増やすことによって向上していくと考えています。
この結果を受け、机上でさらに判定率の向上を目指すか、1回現場で試してみるかという議論になったのですが、環境や製品の状態が変わることも見据えプロトタイプ検査機の製作に踏み切りました。
こちらはプロトタイプの構成です。
くどいようですが、「現場で使えるシステム」を第一に考えています。製造現場にはすでに存在する加工設備や搬送機器が多く存在しています。そしてこれらを制御する機器も存在します。我々にはその制御技術が手の内にあります。ロボットやカメラ、搬送機械もコントロールするノウハウと技術があります。
AIを提案するそれぞれのメーカーが自分たちの仕組みで完結するシステムを提案している場合もあると思いますが、既存のラインをすべて置き換えるのにどれだけ時間がかかるでしょうか。私たちはこういった生産ラインの自動化ノウハウを活かし、プロトタイプのシステム構成を検討してまいりました。
スライドで表示されているようにコンベアから流れてきた対象部品をロボットがピッキングしてカメラにて検査するという流れになります。ロボットやワークを搬送するためのコンベアをPLCと呼ばれる制御機器と接続し、現場の環境を再現しています。
機能推論デバイスにはNVIDIAさんのJetson TX2を採用し、カメラから入力されてくる画像をここで処理しPLCに判定結果を送ります。PLC側からすればOKやNGといった判定結果を受け取ることになるので、その信号次第でロボット等にその後の処理もさせられる仕組みが作れることになります。
ABEJAさんにはAIの学習過程でたくさんのアドバイスをいただき、エッジ側は武蔵主導でAIモデルを実装したプロトタイプを製作、精度の検証を行なってきています。
それでは次にJetsonの中身の構成について説明をしたいと思います。これがJetsonをベースにした弊社のシステムアーキテクチャになります。ここでも製造現場で使用することを想定してこのシステムアーキを考えていますが、大きく4つのモジュールにプログラムが分けられています。
1つ目はセンサー通信部。今はカメラというセンサを接続していますが、今後使っていきたいセンサは画像だけではありません。その場合に接続したいセンサとそれに見合ったプログラムを選択するだけでほかのモジュールの変更がなくてもいいように考えています。
次にデータ保存部ですが、センサから入力したデータを推論部に送りながらも再学習のためのデータとして保存するモジュールとして準備しています。ABEJAプラットフォームのようなクラウドへの転送や社内のオンプレミスサーバがその対象になるかと思います。
推論部ですが、今の時点では最適と思われる推論モデルも明日にはもっといいモデルが現れるかもしれません。こういった状況に対してすぐに最新のモデルのテストが実施でき、より早い段階で最適モデルの採用が反映できる環境を準備しています。
制御機器通信部についても、前述の3つモジュールと同様で各メーカーとの通信インターフェイスに合わせたプログラムが必要になります。さまざまなメーカーのPLCが存在したとしてもすべてのプログラムを作り直す必要はなく、モジュールの入れ替えで対応できる仕組みを構築しています。
このように、近い将来AIがコミュニティ化され、AIをツールとして使用できる時代が来ることを今から想定してこのシステムアーキを構成しています。
次はステップの構想です。こちらは先ほど説明したプロトタイプの構成になっています。ここは武蔵の得意領域です。そして先ほどのシステムアーキテクチャを活かし、次のステップとしてクラウドを活用した付加価値向上を計画しています。
武蔵が得意とするエッジ側の技術をプラットフォーム化し、学習データのアノテーション、学習、そしてデプロイの作業をABEJAプラットフォームを活用することでさらにエッジ側とシームレスに接続、運用できるように進めていきたいと思います。
それではここで我々のプロトタイプの動画を少しご覧いただきたいと思います。
(動画)
プロトタイプにしては少しお金をかけ過ぎた感がありますが。
(会場笑)
3、4ヶ月で作り上げました。データを準備して机上で検証しているだけではわからなかった課題がたくさん出てきています。精度と速度といったようなトレードオフの関係性にある目標をいかに解決するかに日々奮闘しています。「とにかく現場でやってみる」が武蔵流です。
このような感じでロボットを使ってコンベアからワークをピッキングして、カメラのユニットへ搬送します。そしてロボットの第6軸目と呼ばれる手首の軸を回転させながら画像を取得して、そのまま推論にかけて合否判定を受け取ります。
その判定によってコンベアに洗い出しますが、OK判定ならOKレーン、NG判定ならNGレーンへ流れ出す仕組みになっています。
続きまして今後の取り組みです。人工知能の眼による検品自動化というテーマに対し「とにかくやってみる」「頭で考え過ぎず、まずやってみる」ということを第一に、やってみたからこそわかった課題を誰よりも早く掴んでいきたいと思います。
今の時点で掴んだ課題は大きな財産とも思っています。あとは自動車業界で培った経験値を活かし、着実にクリアしていくだけです。やってみなければ課題が何かもわかりません。ほかに負けないスピードと掴む課題を武器に、事業者部品メーカーの新たな領域のチャレンジへつなげていきたいと思っています。
今回動画でお見せしたプロトタイプですが、4月4日から6日にかけて東京ビッグサイトで開催される「第2回AI・人工知能 EXPO」に出展させていただきます。実際に良品のベベルギア、そして傷のついたベベルギアを判別するデモを披露いたしますので、ぜひ足を運んでいただけたらと思います。
最後に武蔵の将来構想をお話ししようと思います。こちらが武蔵のAIロードマップになります。
このたびABEJAさんのAI Professional partnerとして参画させていただくことになりましたが、2017年から始まったABEJAさんとの活動を通じてAIの技術を少しずつ手の内に入れてきています。
今後もABEJAと武蔵は連携を強め、このAIロードマップを実現させていきたいと思っています。プロトタイプの製作もほぼ計画通り進めてきており、今後は実際の製造現場への展開を進めていきたいと思います。
さらには現在建築中の新工場があるのですが、ここにはこれまで培ってきたAI技術を取り入れ、最先端のものづくり現場を実現していくと考えています。
最終的には我々の最大の強みである現場、すなわちハードの力とこの活動で培ってきたソフトの力を融合させ、次世代の生産現場ものづくりを加速させるためのManufacturing platformと呼べるようなシステムを構築していきたいと思っています。
自動車部品の製造メーカーだからこそできる、共感できることを強みにここに来てくださっているみなさんや世界のものづくりのお役に立てることを信じております。
改めて製造現場で求められるAIの価値をまとめたいと思います。まずはなにより人による作業に対しスピード・精度・コストの観点で上回ることが必要になると思います。
これについては今回の活動において十分見通しが持てていますし、今後のソフト・ハードの進化が強力な追い風になることは確実だと考えています。
2つ目として、ものづくりにおいてAIを活用するときにはすでにあるラインへ実装できることが必要不可欠だと思っています。今後いろいろなAIが開発されていくと思いますが、それをきちんと現場で使えるかたちで実装していく技術が重要になっていくと思います。
そして、なによりお客様や製造現場に対する信頼性が必要になります。製造現場でAIが使われるには業界の認知も必要だと思います。それには先の2つの実現があってこそです。私たちは製造業のAIの活用においてフロントランナーとなるべくチャレンジを続けていきたいと思います。
武蔵がここまで成長してこれたのは、ものづくりの現場においてこの3つの価値を高めることを続けてきたからです。80年の歴史の中で培ってきたこの基盤は、AIのような最新技術を使いこなすうえでも大きなアドバンテージだと考えています。
我々には現場があります。世界30カ所のグループ生産拠点への導入ニーズもあります。チャレンジしなければ課題はわかりません。失敗することを恐れず前進して、現場のお役に立てられるようAIの価値をものにしていきたいと思います。
武蔵の未来工場の設立はすぐそこまで来ています。IoT、AI技術をフル活用することでものづくりの現場にイノベーションを起こしてまいりたいと思います。ご静聴ありがとうございました。
(会場拍手)
株式会社ABEJA
2024.10.29
5〜10万円の低単価案件の受注をやめたら労働生産性が劇的に向上 相見積もり案件には提案書を出さないことで見えた“意外な効果”
2024.10.24
パワポ資料の「手戻り」が多すぎる問題の解消法 資料作成のプロが語る、修正の無限ループから抜け出す4つのコツ
2024.10.28
スキル重視の採用を続けた結果、早期離職が増え社員が1人に… 下半期の退職者ゼロを達成した「関係の質」向上の取り組み
2024.10.22
気づかぬうちに評価を下げる「ダメな口癖」3選 デキる人はやっている、上司の指摘に対する上手な返し方
2024.10.24
リスクを取らない人が多い日本は、むしろ稼ぐチャンス? 日本のGDP4位転落の今、個人に必要なマインドとは
2024.10.23
「初任給40万円時代」が、比較的早いうちにやってくる? これから淘汰される会社・生き残る会社の分かれ目
2024.10.23
「どうしてもあなたから買いたい」と言われる営業になるには 『無敗営業』著者が教える、納得感を高める商談の進め方
2024.10.28
“力を抜くこと”がリーダーにとって重要な理由 「人間の達人」タモリさんから学んだ自然体の大切さ
2024.10.29
「テスラの何がすごいのか」がわからない学生たち 起業率2年連続日本一の大学で「Appleのフレームワーク」を教えるわけ
2024.10.30
職場にいる「困った部下」への対処法 上司・部下間で生まれる“常識のズレ”を解消するには
2024.10.29
5〜10万円の低単価案件の受注をやめたら労働生産性が劇的に向上 相見積もり案件には提案書を出さないことで見えた“意外な効果”
2024.10.24
パワポ資料の「手戻り」が多すぎる問題の解消法 資料作成のプロが語る、修正の無限ループから抜け出す4つのコツ
2024.10.28
スキル重視の採用を続けた結果、早期離職が増え社員が1人に… 下半期の退職者ゼロを達成した「関係の質」向上の取り組み
2024.10.22
気づかぬうちに評価を下げる「ダメな口癖」3選 デキる人はやっている、上司の指摘に対する上手な返し方
2024.10.24
リスクを取らない人が多い日本は、むしろ稼ぐチャンス? 日本のGDP4位転落の今、個人に必要なマインドとは
2024.10.23
「初任給40万円時代」が、比較的早いうちにやってくる? これから淘汰される会社・生き残る会社の分かれ目
2024.10.23
「どうしてもあなたから買いたい」と言われる営業になるには 『無敗営業』著者が教える、納得感を高める商談の進め方
2024.10.28
“力を抜くこと”がリーダーにとって重要な理由 「人間の達人」タモリさんから学んだ自然体の大切さ
2024.10.29
「テスラの何がすごいのか」がわからない学生たち 起業率2年連続日本一の大学で「Appleのフレームワーク」を教えるわけ
2024.10.30
職場にいる「困った部下」への対処法 上司・部下間で生まれる“常識のズレ”を解消するには