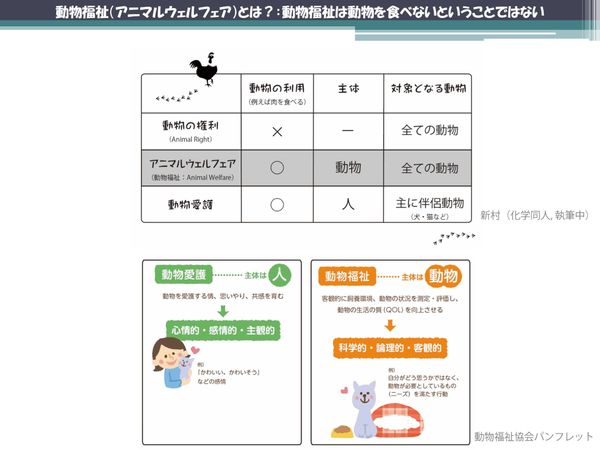
2024.10.10
将来は卵1パックの価格が2倍に? 多くの日本人が知らない世界の新潮流、「動物福祉」とは
提供:株式会社ABEJA
リンクをコピー
記事をブックマーク
村田宗太氏:みなさん、こんにちは。武蔵精密工業、AIプロジェクトの村田です。本日は「AIを活用し、人に代わる検品自動化」を目標にした弊社の取り組みを紹介させていただきます。
それではまず簡単に会社紹介をさせていただきます。動画で紹介いたしますのでご覧ください。
(動画)
音声:1938年の創業以来、独創的な発想と技術力で自動車の重要機能を支えるさまざまな商品を提供し続けてきた武蔵精密工業。その歩みは資源・エネルギーを伝達、変換し、社会に有用な価値を生み出す試行錯誤の歴史でした。
2016年欧州最大手のインフラを装備し、高い鍛造技術と生産能力を持つHAY GROUPが加わり、グローバル供給体制と顧客網を一層強化。武蔵グループはさらなる高みを目指します。
そして今、国内6拠点、海外24拠点、1万5000人を超える従業員からなるグループに成長を遂げた武蔵は新たなグローバルブランドスローガンを掲げます。Power to Value。限りあるエネルギー、多種多様な力をお客様が求める価値へと変換する。この使命を果たすため探求を続ける武蔵グループの姿勢をご紹介します。
武蔵の製品、それは4輪車2輪車の性能を左右する重要部品の数々。高品質、低コスト、環境対応など時代のニーズに応えPower to Valueを体現するラインナップは世界中の自動車・バイクメーカーから高い評価をいただいています。
武蔵の研究開発は先進の施設、設備を備え、設計から機能保証に至るまでをカバー。技術開発の集約拠点武蔵グローバルセンターでは、技術開発力の強化はもちろん、材料研究などの基礎研究も視野に入れた研究開発に取り組んでいます。
武蔵の生産体制、それは商品開発力と並ぶ大きな強み。鍛造から切削、熱処理、仕上げ、組み立てに至る各工程が連結され社内で一貫生産を実現。世界のお客様に信頼される高品質・低コストな商品を提供しています。
そしてHAYの統合を通じ、鍛造技術の向上とともにユニット領域へ製品ラインナップを拡充。相互のシナジーでさらなる事業領域の拡大を目指します。独創的なものづくりから魅力的な商品を。
社会に有用な価値を生み出す。武蔵のその姿勢はものづくりにとどまりません。地域社会へ、環境保全へ、さまざまなかたちで社会への責任を果たすことで持続可能な発展を続けていきます。
多種多様な力を社会に有用な価値へ。Power to Value。武蔵精密工業。
(動画ここまで)
以上が当社の概要になりますが、ここで1つ追加でお話をさせてください。先端技術の紹介の場ではありますが、弊社のDNAを紹介させていただきます。
弊社は今年で創業80周年を迎えます。80年の歴史がある武蔵は昔から企業理念を大事にしております。
精神論だけのようにも思えますが、私は現在のアジャイル開発やデザインシンキングに通ずるものがあると思っています。
時代の変化をバネにして変革に挑戦し、アイデアを形にするところから始め、悩んだときにはここに立ち戻り「とりあえず前に進もう」「やってないことからやってみよう」という気持ちに切り替えてAIプロジェクトを推進しています。
それではAIプロジェクトの紹介をさせていただきます。弊社のAI活動の経緯を紹介いたします。私ごとではありますが、AIの活動をする前は製造現場で使用される設備の設計・製作をする部署にいました。
ある日突然、社長に呼ばれて、私は「なにかしでかしたか!?」と思いましたが、社内にいるソフトエンジニアが招集されており、「武蔵でもAIを使ってなにかできないだろうか?」という議論が始まりました。
たくさんのアイデアが出ましたが、製造現場の永遠の課題、目視検査がテーマとして挙げられ、対象部品をベベルギヤに定めて研究が開始されることになりました。
2017年2月に受講させていただいたABEJAさん主催のディープラーニングセミナーで学んだことを活かして、ディープラーニング自体のスキルを社内に作りながらも、私の過去の経験と合わせてすぐにプロトタイプの製作に入ります。そうは言ってもチームのメンバーは本職と兼業の状態でした。もちろん私も同様です。
それにもかかわらず、アイデア出しから始まった企画は、わずか1年足らずで専任の組織が設立され、今ではさらにスピードを上げて活動を進めています。
ここで取り組みの対象として選んだベベルギヤについてご説明させていただきたいと思います。自動車の左右のタイヤの間にはデファレンシャルという部品が組み込まれています。これは自動車がカーブするときに適正な回転差をつけてトルクを配分する機構で、その構成部品がベベルギヤです。
日本語では「かさ歯車」と言います。非常に大きな力を受けるギヤですので、強度と歯型の精度が高いレベルで求められる重要部品になっています。当社ではこのベベルギヤをグローバルで年間4,000万個ほど作っています。
次に取り組みの詳細を説明させていただきたいと思いますが、まずはAIを使う前の従来の取り組み事例から紹介させていただきます。これはAIを使う以前、というよりも武蔵が製造現場で現在も使用している検査技術になっていますが、今回の取り組みに非常に深い関係があるので紹介したいと思います。
まず自動車部品がどのように作られているかを紹介いたします。ベベルギヤを対象に製造工程が表示されています。
材料を切断するところから始まり、鍛造と呼ばれる工程に移ります。鍛造工程では大型プレスによって鉄の塊を金型の形状にプレスしますが、武蔵のベベルギヤは精密鍛造によって成形されているのが特徴で、ギヤ部切削加工はありません。
その後、鍛造工程で発生したバリを除去し、ギヤの反対側を旋盤加工にて切削加工し、硬度を高めるための熱処理工程を経て、最終的に作業者の目視による外観検査が実施されます。
部品によって工程系列はさまざまですが、ベベル以外の製品についてもこの外観検査と呼ばれるものは必ずあり、多くの作業者を必要としています。ベベルの生産数は国内だけでも月産130万個、最終工程での不良率は0.002パーセント程度です。
これは日に不良が1、2個出るかどうかくらいの割合になっています。本当にわずかな不良を見つけ出さなければならないため熟練者の技量が必要ということと、その負担は計り知れません。
では「どんな不良を見つけているのか」と言うと、製造工程の製品を搬送する過程で発生してしまう打痕と呼ばれるギヤの歯先についた傷のようなもの、鍛造工程で発生するシワのような不良です。
別の製品のカムシャフトですと、鋳造と呼ばれる工程があり、その方法で素材を作り出すときに溶かした鋳鉄を鋳型に流し込む際に発生する気泡により、右の写真のように小さな穴が発生します。
これを業界用語で「巣穴」と呼んでいます。このような不良が対象になります。
もちろんこれはごく一部の不良ですので、不良の種類はもっとたくさんあります。ここで言いたいのは、非常に小さな欠陥も見逃すと自動車に組み込まれたあと、大きな事故につながる可能性があるということです。
先ほどのスライドのような流出することのできない欠陥を、現在は人の五感に頼っていますが、習熟度のばらつきや長時間にわたる高負荷作業が課題とされています。
そんな作業をベベルギヤの場合は最短2秒で検査しなければなりません。非常に難しい検査であるがゆえ、人間の高い適応力に支えられているのが現状となっています。
ここからは「従来の取り組みの詳細」をご紹介いたします。弊社としても過去から多くの目視検査の自動化を進めてきておりますが、多種多様な部品に対する外観検査は長年のテーマとなっています。
その一例が「カムシャフト外観検査設備」です。カメラとそのサプライヤーが提供しているコントローラと照明機器により検査を実施しています。
この設備も私が開発を進めて現場に導入したのですが、設備を作るうえでは今まで培ってきた独自のノウハウを詰め込んでおり、肝のカメラユニットはメーカーからの購入品となっております。
セット販売されている画像処理ユニットを使用した経験がある方はご存知かもしれませんが、準備された機能を選び検査するエリアを設定して、そして閾値を決めて検査を実施するという流れになります。
メリットは比較的簡単にセットアップできるところですが、従来の設備の弱点・限界点としては、特定の不具合事象に特化した機能になってしまうこと、閾値設定が非常に難しいという点が挙げられます。
この点は、我々のような設定する側のエンジニアにとっても、この設備を使用する現場にとってもぬぐいきれない課題、解決したい課題として持ち続けていました。
こういったジレンマを抱えていたこともあり、ディープラーニングの可能性に大きな期待を抱いてプロジェクトがスタートされることになりました。
前置きが長くなってしまいましたが、ここからは現在の取り組みについてご紹介したいと思います。
改めてチームの紹介をさせていただきたいと思いますが、冒頭でプロトタイプの製作を開始していると言った通り、我々の強みは自社に各方面のエンジニアがいることです。
プロトタイプの製作をすべて自社で行っております。だからこそスピード感を持って推進できていると自負していますが、AIの可能性を机上で検証するだけではなく、いち早く製造現場で使用するためにディープラーニング開発エンジニアから設備設計、制御エンジニアまでプロジェクトメンバーとして招集しております。
ここにABEJAさんのディープラーニングに対する深い知見を融合していただき、お互いの強みを活かして開発を進めています。先ほどABEJAの岡田さんはオタクではないと言っていましたが、ABEJAさんと武蔵はスーパーオタクの集団です。
(会場笑)
このオタクの集団で形成されたチームは、ものづくりの現場にAIを導入するべく志をともにしていつも本当に楽しく仕事をさせていただいています。
取り組みの方向性ですが、「自動車業界のAI活用」というとリスクもあると思います。弊社としても同様で、ものすごく小さい欠陥も許されない状況で検査には「傷なきこと」といった精度が求められます。
我々の取り組みも現場の人による検査をすぐになくすわけにはいかないかもしれません。検査工程にAIを使用するということはお客様の同意も必要になってきます。
ですが「世の中が変わってからAIの開発をしていては遅い」と思っています。コスト、精度、スピードの点においてAIの検査がいずれ人の能力を上回ることを探求して、AIをツールとして使いこなす研究を進めて行きたいと思っています。
これは我々の目標値です。人と同等以上の能力の実現を目指して、NG品の検出精度100パーセント。検査時間は2秒を掲げています。非常に高い目標値ですが、現場で効果を出すためには必要な数字と考えています。
それでは現在の取り組みの成果をご紹介いたします。まずデータ取りのための準備からですが、対象の検査部品をチャックさせて、回転させるためのロボットアーム、そして比較的安価なGigEタイプの産業用カメラとLEDの照明2点で構成しました。
教師データは先ほどの設備から収集した画像8万6000枚ほど取得いたしました。
背景が青いのにも理由がありますが、ここではノウハウの一部としてとどめさせていただきます。
アノテーションです。ベベルギアの不良の種類はたくさん存在するので、発生頻度にかかわらずアノテーションツールにはすべての不良が準備されています。
今後、不具合の分類や分析等も見据え、アノテーションツールをABEJAさんに作成いただきました。
具体的な方法としては各画像に対してまず不良があるかないかの確認をします。不良がある場合には不良ポイントをマーキングして、不良内容を選択することで対象の画像へのタグ付けが完了することになります。
このアノテーション方法を採用することで画像全体としてのタグと不良箇所の位置情報の2つを同時に紐付けることができると思っています。その後、ファイル整理や紐付けを意識することなく進められることになります。この1回のアノテーションにて、さまざまなAIアルゴリズムに対応できると思います。
株式会社ABEJA
2024.11.13
週3日働いて年収2,000万稼ぐ元印刷屋のおじさん 好きなことだけして楽に稼ぐ3つのパターン
2024.11.11
自分の「本質的な才能」が見つかる一番簡単な質問 他者から「すごい」と思われても意外と気づかないのが才能
2024.11.13
“退職者が出た時の会社の対応”を従業員は見ている 離職防止策の前に見つめ直したい、部下との向き合い方
2024.11.12
自分の人生にプラスに働く「イライラ」は才能 自分の強みや才能につながる“良いイライラ”を見分けるポイント
2023.03.21
民間宇宙開発で高まる「飛行機とロケットの衝突」の危機...どうやって回避する?
2024.11.11
気づいたら借金、倒産して身ぐるみを剥がされる経営者 起業に「立派な動機」を求められる恐ろしさ
2024.11.11
「退職代行」を使われた管理職の本音と葛藤 メディアで話題、利用者が右肩上がり…企業が置かれている現状とは
2024.11.18
20名の会社でGoogleの採用を真似するのはもったいない 人手不足の時代における「脱能力主義」のヒント
2024.11.12
先週まで元気だったのに、突然辞める「びっくり退職」 退職代行サービスの影響も?上司と部下の“すれ違い”が起きる原因
2024.11.14
よってたかってハイリスクのビジネスモデルに仕立て上げるステークホルダー 「社会的理由」が求められる時代の起業戦略